sheet metal forming processes factories Also known as sheet metal fabrication, sheet metal forming uses metal sheets to make various products and components. The metal sheets are formed and cut into the necessary shape and size via many different . Metal roofing is durable and comes in a wide range of styles, making it a top choice for homes. The different types of metal roofs can be categorized .
0 · sheet metal working process pdf
1 · sheet metal stamping process pdf
2 · sheet metal processes pdf
3 · sheet metal forming process pdf
4 · sheet metal forming press dies
5 · sheet metal forming by hand
6 · sheet metal bending process pdf
7 · bulk deformation vs sheet metal forming
Find the proper measurement for your gauge size. This chart compares gage numbers to their steel and aluminum sizing standards.
Also known as sheet metal fabrication, sheet metal forming uses metal sheets to make various products and components. The metal sheets are formed and cut into the necessary shape and size via many different . 1. The different types of sheet metal forming processes such as bending, stretching, and deep drawing. 2. The materials used in sheet metal forming, including commonly used metals, alloys, and composites. 3. The .
In this blog, we dive into seven key sheet metal forming processes that shape modern manufacturing: Laser Cutting, Water Jet Cutting, Stamping, Welding, Roll Forming, Spinning, and Rolling. Keywords: Sheet Metal Forming processes; Forming Process Parameters; Springback; Finite Element Simulation. 1. Introduction Sheet metal forming in its basic sense means the stretching of sheet blank between a punch and a die. * Corresponding author.Explore the intricate process of sheet metal forming, its applications in various industries, and the distinction between sheet and plate metal. Learn about the manufacturing processes, the challenges with plate metal, and the final .
•Hydro-forming – cheap tooling, no net thinning, slow, high formability Material stretched into shape •Stretch forming – very cheap tooling, net thinning, slow, low formability •Super-plastic forming – cheap tooling, net thinning, expensive sheet metal, slow, very high formability Technology – a brief review Forming Speed 20 . Forming is the most widely used sheet metal operation used for manufacturing various sheet metal components across the industry.. Sheet Metal Forming . Image courtesy: Wiki Based upon the manufactured components and the manufacturing process, various kinds of forming are developed.. Different types of sheet metal forming processes and their .
Incremental sheet metal forming (ISMF) has demonstrated its great potential to form complex three-dimensional parts without using component-specific tools against the conventional stamping operation.
For sheet metal forming process, the most used test in the literature today is the Strip Drawing Test or Bending Under Tension (BUT) Test shown in Figure 8. The test consists of bending a sheet metal strip through a pin of predetermined radius and on this pin to make the sheet slide. . Klocke F. Manufacturing Processes 4 - Forming (RWTH . Sheet Metal Forming Processes. There are a variety of core manufacturing processes used to form sheet metal into parts. The techniques deployed depend on the geometries and production volumes needed, as well as the formability of the selected metal. . Sheet metal laser cutting is a manufacturing process to cut sheet metal materials using a .Sheet metal forming is highly prevalent in manufacturing. Sheet metal parts can be discovered in a broad spectrum of applications, such as in the automotive sector, aerospace field, consumer goods, and household appliances. . Hydroforming is a specialized sheet metal forming process that utilizes high-pressure hydraulic fluid to shape the .
Metal forming is a process of manufacturing components of desired shapes by deforming the material plastically, by the application of compressive force, bending or shear force, tensile force, or combinations of these all forces together, without adding or removing material. . Stretch forming is a sheet metal forming process in which the sheet .
The forming limit diagram is a useful reference for sheet metal manufacturers. Sheet Metal Classification . There are 3 major classes of processes of sheet metal working. Cutting: Cutting is the use of shearing forces to remove material from a work piece. Technically not a metal forming process, but of extreme industrial importance.Metal forming processes Metal forming: Large set of manufacturing processes in which the material is deformed plastically to take the shape of the die geometry. The tools used for such deformation are called die, punch etc. depending on the type of process. Plastic deformation: Stresses beyond yield strength of the workpiece material is required. Consistency and Reproducibility: Metal forming processes are highly controllable, which ensures consistent quality and repeatability in mass production settings. Disadvantages of Metal Forming. High Initial Costs: The tooling and setup required for many metal forming processes, such as stamping and extrusion, can be costly. These initial .Unlock the full potential of your manufacturing processes with our comprehensive guide to sheet metal fabrication. Dive into the details of transforming flat metal sheets into high-quality, functional parts and products. From cutting-edge techniques to best design practices, this guide is crafted to address the unique challenges faced by industry professionals. Whether you’re seeking to .
If you are looking for sheet metal forming for your manufacturing needs in the areas of telecommunications, retail store fixtures, computers, electronic data racks and enclosures, industrial products, medical devices, and commercial .
BENDING Bending of sheet metal is a common and vital process in manufacturing industry. Sheet metal bending is the plastic deformation of the work over an axis, creating a change in the part's geometry. Similar to other . In this manuscript, we present a comprehensive overview of true digital twin applications within the manufacturing industry, specifically delving into advancements in sheet metal forming. A true digital twin is a virtual representation of a physical process or production system, enabling bidirectional data exchange between the physical and digital domains and . Stamping is a manufacturing process that involves pressing or forming sheet metal or other materials using a die and a press. This technique is used to create a wide range of components, from small intricate parts to large panels, in industries like automotive, electronics, and appliance manufacturing, due to its efficiency and precision.
Research and development in sheet metal shaping requires knowledge within several disciplines, including materials, tribology and processing, as well as knowledge of the equipment for testing and verification. Swerim has depth knowledge in the field and good access to lab equipment. Process, methods and materials for sheet metal forming
Sheet Metal Bending is a pivotal process in the realm of sheet metal forming, crucial for shaping metal into desired angles and forms without compromising the material’s integrity. It utilizes force to manipulate metal around a single axis, yielding precise, clean bends along a predetermined bend line that are fundamental in manufacturing diverse products.
The main sheet metal forming processes covered are tube bending and forming as well as bending of sheet and plate. Tube bending can be done via press bending, rotary drawing, heat induction, roll bending, and sand packing. . “Bending is a manufacturing process that produces a V-shape, U-shape, or channel shape along a straight axis in .FluidForming is a cost-effective sheet metal forming process designed for rapid prototyping & low- to medium-volume production. 800-497-3545. . FluidForming Americas is a quality-driven sheet metal forming company that offers manufacturers a cost-effective way to quickly — and with unbeatable levels of accuracy and repeatability — produce . In sheet metal forming processes there is still a lack of knowledge in this field mainly due to the need of a proper modelling of sustainability issues and factors to be taken into account. . Calculation of carbon emissions in metal forming manufacturing processes with eco-bening lubrication. Trans. Namri/Sme, 38 (2010), pp. 751-758. View in .

Sheet Metal Forming - Download as a PDF or view online for free. . Stretch Forming ME 4210: Manufacturing Processes and Engineering 14 Prof. J.S. Colton 70. STRECTH FORMING • In most operation blank is rectangular sheet, clamped along narrow edges and stretched length wise. • Controlling amount of stretch is important to avoid tearing.Deep drawing is a sheet metal forming technique in which a sheet metal blank is mechanically dragged radially into a forming die by the action of a punch. As a result, the process is a sharp transformation with material retention. When the depth of the drawn component exceeds its diameter, the technique is referred to as "deep drawing" Although the advantages of formability are notable, blow-forming processes, which are classified as sheet metal stretching processes, present limits in terms of uniformity of the thicknesses of the produced product.
2. Deformation . Sheet metal deforming processes involve changing and processing sheet metal without cutting it. Bending is one of the most critical forming processes, and it can be done using a brake machine.A sheet metal company can use this tool to bend sheet metal into V, U, and channels up to 120 degrees.
sheet metal working process pdf
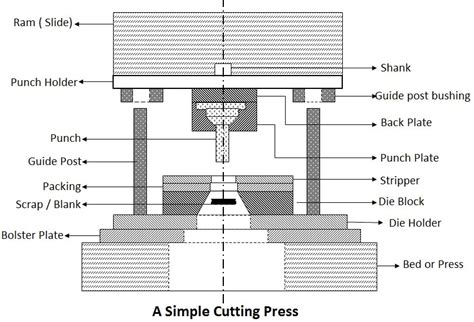
deck electrical box covers
dc power junction box
If there is crawlspace with access above said room those boxes are still "accessible". Some instances you could even put in an access cover of some sort if you don't want to expose said boxes, or make them flush with wall/ceiling and put blank covers on them, then they are accessible.
sheet metal forming processes factories|sheet metal processes pdf