forming sheet metal Sheet Metal Forming and Slide Forming Department Valco Valley Tool & Die is your global source for metal parts manufacturing in Cleveland, Ohio. Recognized for our upstanding reputation for quality products, services, and . CNC programming (Computer Numerical Control Programming) is a crucial aspect of modern manufacturing that enables computer-controlled machines to perform precise and complex tasks.
0 · sheet metal layout drawings
1 · sheet metal forming types
2 · sheet metal forming process pdf
3 · sheet metal forming press dies
4 · sheet metal forming pdf
5 · forming sheet metal by hand
6 · forming process in sheet metal
7 · bulk deformation vs sheet metal forming
CNC programming refers to the process of using software to develop CNC machine instructions. These instructions control how the CNC machine moves while interacting with the work piece. Popular CNC machines that work with CNC programming are CNC lathes and CNC milling machines.
sheet metal layout drawings
What is Sheet Metal Forming? Also known as sheet metal fabrication, sheet metal forming uses metal sheets to make various products and components. The metal sheets are formed and cut into the necessary shape .Forming of shallow parts using rubber tools. Maziar Ramezani, Zaidi M. Ripin, in Rubber-Pad Forming Processes, 2012. 4.1 Introduction. Sheet metal forming is a costly manufacturing process that is widely used in different industries. Many small companies are required to manufacture curved products and shallow parts with fine details in a small lot size which leads to both a .
Sheet metal expanding is a specialized process within sheet metal forming that involves stretching the metal to create a mesh-like pattern. This technique enhances the flexibility and strength of the sheet metal, making it suitable for various applications, including filtration, screening, and architectural details.
değişken devir cnc torna
Sheet Metal Forming and Slide Forming Department Valco Valley Tool & Die is your global source for metal parts manufacturing in Cleveland, Ohio. Recognized for our upstanding reputation for quality products, services, and .กลุ่มกระบวนการขึ้นรูปโลหะแผ่น (Sheet Metal Forming Process) และถ้าวัสดุเริ่มต้นมีลักษณะเป็นก้อน (Bulk Metal Forming Process) จะเป็นกระบวนการขึ้นรูปโลหะก้อน Desktop Metal, Inc. (NYSE: DM) introduces the Figur G15, the first commercial platform of its kind to shape standard sheet metal on demand directly from a di.General Forming Corp. 640 Alaska Avenue, Torrance, California 90503, United States. [email protected] (310) 326-0624
Forming Sheet Metal. Forming sheet metal is usually done either by drawing the metal or by pressure forming the metal. When drawing metal, the die engineers must ensure that the metal flows, as it's being formed, in such a way as to not leave weak areas. What the part engineers look for is even metal thickness on the entire finished part. Before we go deeper, we should learn about what sheet metal is. Sheet metal fabrication is forming metal into thin, flat sheets. This can be done through various methods, including stamping, cutting, bending, etc. Sheet metal is used in many applications, from automotive body panels to electronic enclosures. Businesses need access to .
Air-Powered Sheet Metal Forming Hammers. These air-powered tools remove dents, smooth out ridges, and shape sheet metal more efficiently than manual hammers. Forming Spoons. Place against the face of your workpiece and strike with a hammer. The blow will transfer to the workpiece without damaging the finish. One of the key advantages of sheet metal hydroforming is its ability to produce parts with reduced material waste and cost savings compared to traditional forming methods. The process allows for the use of thinner materials while still maintaining the required strength, which can result in lighter parts and lower production costs.
What Is Sheet Metal Forming? Sheet metal forming entails taking thin, flat sheets of metal and manipulating them into fully formed 3D structures. The process transforms a basic raw material into complex finished products using an array of manufacturing techniques. Conceptually, it works much like assembling a puzzle – the final 3D shape is . Sheet metal forming is an essential process used in industries such as automobile construction and manufacturing. It involves shaping flat sheets of metal into three-dimensional objects. This guide explores the beginning to end application process and covers forming techniques, equipment, challenges, and materials involved. Here are several other benefits of robotic incremental sheet forming: Precision: automation produces more consistent results than manual processes, reducing scrap rates. In addition, as the geometry is produced incrementally, there is no springback as you may find with other sheet metal forming processes. In this video we will discuss three basics to sheet metal forming. For more information visit www.rapidmanufacturing.com
Sheet metal forming is a manufacturing process that involves shaping thin metal sheets into desired geometries through techniques like bending, stretching, and deep drawing. This versatile process is widely used in industries such as automotive, aerospace, and construction, due to its efficiency in producing lightweight and durable components.. Familiarizing yourself with sheet .Sheet Metal Stretch Forming “Blue Streak” Forming Process. Equipment. Verson Deep Draw Press. 400 ton, 60” x 119”, 200 ton cushon. CNC Brake Press. 90 ton, 120”, 7-axis. Titanium Hot Form Press X2. 90 ton, 30” x 60”, 1500 deg Heated .
Sheet metal forming, also known as metal fabrication, encompasses a range of techniques for transforming flat metal sheets into diverse shapes and configurations. The significance of sheet metal forming lies in its .
The FluidForming sheet metal forming process accommodates integrated logos, undercuts, organic forms, deep drawn parts, and even components with curves that would be likely to wrinkle or tear with traditional metal forming methods. FluidForming sheet metal forming is designed for low- to medium-volume parts production.
The multi-step forming process is a sophisticated technique for achieving large-radius bends in sheet metal using smaller radius punches. This method’s fundamental principle involves segmenting the desired arc into multiple polyline sections, as illustrated in Figure 1.View Pro - Forming Sheet Metal (www.pro-forming.com) location in Connecticut, United States , revenue, industry and description. Find related and similar companies as well as employees by title and much more. Products. Sales Contact & Company Search Sales Automation Conversation Intelligence Workflows.Sheet metal forming processes are those in which force is applied to a piece of sheet metal to modify its geometry rather than remove any material. The applied force stresses the metal beyond its yield strength, causing the material to plastically deform, but not to fail. By doing so, the sheet can be bent or stretched into a variety of complex shapes. Sheet metal forming is a core element in the crafting of products from cars to appliances – involving skill, experience and technologically advanced tools. This article provides an insight into how this intricate process works, discussing techniques used with metals to create superior quality components.

Traditional sheet metal forming is a capital- and time-intensive process that requires an expensive stamping press, which often costs about million, as well as tools and dies that take months to produce. While similar processes such as hydroforming, fluid cell presses, and zinc low-cost die tooling aim to reduce the time of forming sheet .Sheet metal forming involves deforming metal sheets plastically, meaning the material is shaped permanently without breaking or cracking. The sheet is subjected to forces beyond its elastic limit, causing it to take a new form. The success of the process depends on several factors, including: Bump forming also known as bump bending, step bending, or repetitive v-bending, is a popular sheet metal fabrication art of bending sheet metal materials into desirable cylindrical or conical shapes for different industry applications using a press brake.. In this article, we provide a comprehensive guide on sheet metal bump bending with details on the suitable metals you .
Forming The sheet metal shaping has been accomplished for thousands of years (and it is carried out still nowadays!) through the hammering technique. The sheet is positioned on metal, wood or metal equipment, which reproduces the shape to be obtained, then through successive hammering it is «obliged» to adhere to the equipment reproducing its . Since the semi-finished product is a sheet or a plate the specimen's thickness typically varies between 1 mm and 5 mm.In most cases the intention of the sheet-bulk metal forming processes is to form local shape elements with dimensions of a magnitude similar to the sheet thickness, projecting out of the plane of the sheet.
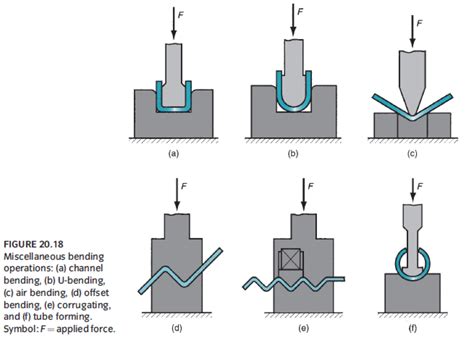
density of steel sheet metal
Swiss machining, also known as Swiss turning, is a high-precision CNC machining process performed on a special type of turning machine designed specifically to produce small and intricate parts.
forming sheet metal|sheet metal forming press dies