aluminum skin on fabric wing There are aluminum wing airplanes with stressed skin AND fabric covering. The Ercoupe has an alum cantiliver wing but the stressed skin only is applied around the leading edge to make a D torque box.. The aluminum rib bays behind the spar are open and covered with . TulAmmo 7.62x39mm ammunition is an economical and reliable choice for both sport shooting and hunting with bolt-action and semi-automatic rifles and carbines. This 7.62x39mm cartridge keeps its qualities under various climatic and weather conditions independent of the season and at a temperature from -20C to +50C (-4F to +122F).
0 · wings made from aluminum
1 · wing skin design
2 · why are wings made with aluminium skin
3 · why are wings made from aluminum
4 · boeing wing skin
5 · aluminum skin for aircraft
6 · aluminum aircraft wings
7 · aluminium wing skin
Custom Rolled Tubing Rings by Midwest Metal Products - the leading manufacturer of rolled tubing angle rings and rolled structural shapes.
There are aluminum wing airplanes with stressed skin AND fabric covering. The Ercoupe has an alum cantiliver wing but the stressed skin only is applied around the leading edge to make a D torque box.. The aluminum rib bays behind the spar are open and covered with .
Replacing the Fabric with aluminum skins ruins a 48 IMHO. It will slow the aircraft speed by as much as 15 miles per hour. The wing will stall differently, and it is heavier. On fabric wings, the upper surface actually rises between the ribs and creates more lift. Metal does not allow for this to happen. With today's fabric materials, it is not . The majority of fighter jets have their skin made out of aluminum, usually 7000 series. Thickness is 1.5-3 mm, a bit thinner than passenger airliners have. Fighters rely on their internal longerons rather than skin for global .The wing skin on an aircraft may be made from a wide variety of materials such as fabric, wood, or aluminum. But a single thin sheet of material is not always employed. Chemically milled .
The skin of an aircraft is the outer surface which covers much of its wings and fuselage. The most commonly used materials are aluminum and aluminium alloys with other metals, including .
When intact, the skin can take a tremendous amount of force without breaking. But as soon as a crack or hole begins, the entire structure is compromised. Contrast this with a fabric-and-tube airplane, most of which will . To lower the weight of his designs, Junkers reduced the skin to the corrugated panels and did away with the smooth skin on top, and he switched from steel to aluminum, a material which he initially avoided to reduce cost.
non metallic electrical enclosures
wings made from aluminum
On a fabric plane, skin damage is just that, as the structure is totally internal. This is one reason many WWII aircraft retained fabric control surfaces. A 30mm cannon hole shot in a . Wings are designed as a complex structure of spars and ribs, clad with aluminum, titanium, or new composite sheathing, or in the fabric, in the early planes. The Frame has been designed to support all the loads, bending . There are aluminum wing airplanes with stressed skin AND fabric covering. The Ercoupe has an alum cantiliver wing but the stressed skin only is applied around the leading edge to make a D torque box.. The aluminum rib bays behind the . Replacing the Fabric with aluminum skins ruins a 48 IMHO. It will slow the aircraft speed by as much as 15 miles per hour. The wing will stall differently, and it is heavier.
On fabric wings, the upper surface actually rises between the ribs and creates more lift. Metal does not allow for this to happen. With today's fabric materials, it is not uncommon for internal structural components to actually need repaired long before the fabric deteriorates. The majority of fighter jets have their skin made out of aluminum, usually 7000 series. Thickness is 1.5-3 mm, a bit thinner than passenger airliners have. Fighters rely on their internal longerons rather than skin for global strength, so the skin is lightly loaded and not structurally essential.
The wing skin on an aircraft may be made from a wide variety of materials such as fabric, wood, or aluminum. But a single thin sheet of material is not always employed. Chemically milled aluminum skin can provide skin of varied thicknesses.The skin of an aircraft is the outer surface which covers much of its wings and fuselage. The most commonly used materials are aluminum and aluminium alloys with other metals, including zinc, magnesium and copper.
When intact, the skin can take a tremendous amount of force without breaking. But as soon as a crack or hole begins, the entire structure is compromised. Contrast this with a fabric-and-tube airplane, most of which will fly fine with fabric only on the wings. To lower the weight of his designs, Junkers reduced the skin to the corrugated panels and did away with the smooth skin on top, and he switched from steel to aluminum, a material which he initially avoided to reduce cost.
On a fabric plane, skin damage is just that, as the structure is totally internal. This is one reason many WWII aircraft retained fabric control surfaces. A 30mm cannon hole shot in a fabric aileron was just a hole as long as it didn't hit a spar. Wings are designed as a complex structure of spars and ribs, clad with aluminum, titanium, or new composite sheathing, or in the fabric, in the early planes. The Frame has been designed to support all the loads, bending moment of . There are aluminum wing airplanes with stressed skin AND fabric covering. The Ercoupe has an alum cantiliver wing but the stressed skin only is applied around the leading edge to make a D torque box.. The aluminum rib bays behind the .
Replacing the Fabric with aluminum skins ruins a 48 IMHO. It will slow the aircraft speed by as much as 15 miles per hour. The wing will stall differently, and it is heavier. On fabric wings, the upper surface actually rises between the ribs and creates more lift. Metal does not allow for this to happen. With today's fabric materials, it is not uncommon for internal structural components to actually need repaired long before the fabric deteriorates. The majority of fighter jets have their skin made out of aluminum, usually 7000 series. Thickness is 1.5-3 mm, a bit thinner than passenger airliners have. Fighters rely on their internal longerons rather than skin for global strength, so the skin is lightly loaded and not structurally essential.The wing skin on an aircraft may be made from a wide variety of materials such as fabric, wood, or aluminum. But a single thin sheet of material is not always employed. Chemically milled aluminum skin can provide skin of varied thicknesses.
The skin of an aircraft is the outer surface which covers much of its wings and fuselage. The most commonly used materials are aluminum and aluminium alloys with other metals, including zinc, magnesium and copper. When intact, the skin can take a tremendous amount of force without breaking. But as soon as a crack or hole begins, the entire structure is compromised. Contrast this with a fabric-and-tube airplane, most of which will fly fine with fabric only on the wings. To lower the weight of his designs, Junkers reduced the skin to the corrugated panels and did away with the smooth skin on top, and he switched from steel to aluminum, a material which he initially avoided to reduce cost.
On a fabric plane, skin damage is just that, as the structure is totally internal. This is one reason many WWII aircraft retained fabric control surfaces. A 30mm cannon hole shot in a fabric aileron was just a hole as long as it didn't hit a spar.
non metallic outlet and device boxes nema os2
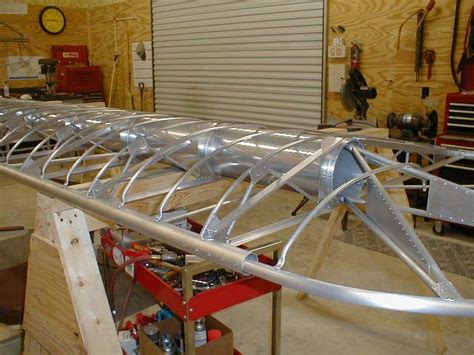
wing skin design
non metallic enclosure nema
why are wings made with aluminium skin
Trump's strategy centered on shielding U.S. steel mills from foreign competition with a 25 percent tariff imposed in March 2018. He also promised to boost steel demand through major investments.
aluminum skin on fabric wing|wing skin design