sheet metal cover process design The manufacturing & design guide. Learn how to effectively design sheet metal parts. This guide starts with the basics and moves toward design best practices and advice on material . I am new to MIG welding and have been making my own gym equipment using mild steel box section tubing. Most of the connections for this equipment comprise of 10mm plate .
0 · sheet metal parts design guide
1 · sheet metal manufacturing guide
2 · sheet metal manufacturing blueprint
3 · sheet metal making process
4 · sheet metal fabrication process
5 · sheet metal cutting process
6 · sheet metal cutting design
7 · how to design sheet metal
Metal tubing, in this case rectangular tubing is true to dimension to the outside, listed as HxWxthickness. Thickness in the US is listed as a decimal, not fraction. So 2x4x.120 will be 2x4 on the outside with a wall thickness just shy of 1/8 .

Sheet metal covers are designed to protect their contents from moisture, light, contaminants, electrical currents, and human contact. They are used to keep components separate, organized, and protected from .The manufacturing & design guide. Learn how to effectively design sheet metal parts. This guide starts with the basics and moves toward design best practices and advice on material . Hole and slot in sheet metal design. 1. The minimum hole diameter should be ( Dmin) ≥ the thickness of the sheet metal ( at least equal to sheet thickness). 2. Proper spacing between the two holes center in a sheet panel .Geomiq's Sheet Metal design guide helps you with your design process to accelerate production time and reduce production costs.
The sheet metal fabrication process consists of two main processes; forming and cutting. These two techniques work together to create the final form of any product. While cutting is a simple process, forming has further .
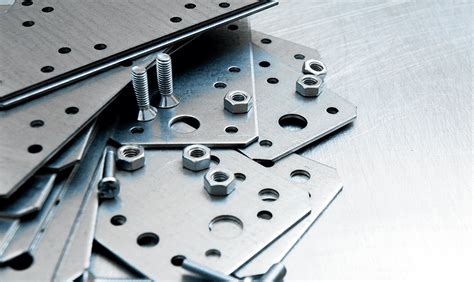
Sheet metal fabrication is the process of forming parts from a metal sheet by punching, cutting, stamping, and bending. 3D CAD files are converted into machine code, which controls a .BEST PRACTICES. TIPS AND TRICKS FROM THE SHOP FLOOR. TABLE OF CONTENTS. I. PART FEATURES. Gusset .
This white paper explores the key components of sheet metal fabrication, ranging from the processes to materials, finishes, design tips, and more.Deciding to use—or simply consider—sheet metal for an application is the first step in a process. The process begins, of course, with function, which in turn dictates design. Choosing a material and gauge are critical steps that involve .FabChat Ai™, your go-to AI companion for all things sheet metal design! Whether you're a seasoned mechanical engineer or a budding product developer, FabChat Ai™ is here to streamline your sheet metal part design process. FabChat Ai™ .Precision is such an important aspect of our company that we put it right there in our company name. Dongguan Jiatong Precise Metal Products Co. is a professional sheet metal fabricator providing customers with a comprehensive range of sheet metal fabrication solutions, including cutting, forming, welding, finishing, silk screening, and assembly.Facility Founded in 2011, .
sheet metal parts design guide
Die design handbook: a practical reference book on process analysis, product design, metal movements, materials, and proved die designs for every class of sheet-metal pressworking by American Society of Tool and Manufacturing .The processing and manufacturing process of sheet metal covers includes design drawings, material procurement, cutting, bending, welding, grinding, surface treatment and other steps. Through this series of fine processes, a cover product that meets the requirements can be produced. In terms of material selection, commonly used sheet metal . A general definition is the parts with constant thickness in the processing process. For any sheet metal part, it has a certain processing process, which is the so-called process flow. The following describes the basic process flow of sheet metal design and processing: Sheet metal processing is also called sheet metal processing.
Through simulation and analysis, the whole process of metal plastic forming can be understood, including the information of material filling die in each stage of metal forming process, material deformation trend, internal stress, strain, strain rate, forming load and velocity vector field, so as to provide scientific guidance for the design of . In this article, we delve into essential tips for sheet metal design, exploring techniques to minimize errors and optimize processes. From blanking to bending, each step is crucial for achieving precise, cost-effective results. . the technology used in the blanking process also varies. The upper cover of the motor controller and other .Sheet Metal Design for Manufacturing. Design parts with the sheet metal fabrication process in mind. Reduce cost and get parts on your desk faster! Learn about the following best practices when designing sheet metal parts: Hems & Offsets; Notches & Tabs; Corners & Welding; Uniform Thickness and more! Process Control for Sheet-Metal Stamping presents a comprehensive and structured approach to the design and implementation of controllers for the sheet metal stamping process. The use of process control for sheet-metal stamping greatly reduces defects in deep-drawn parts and can also yield large material savings from reduced scrap.
The sheet metal process and the structural design of sheet metal parts are inseparable. It is necessary to closely combine the sheet metal process, improve the structural design level of sheet metal parts, and design the structural parts with processing technology, so as to reduce the production cost and improve the production efficiency.
This die is custom-made to punch out the desired shape from the metal sheet and is installed in a metal stamping process. The die consists of two main parts: the punch and the die cavity. The metal sheet is positioned between these components, and the punch exerts force to push the material into the die cavity, cutting it into the intended shape.
Learn the Basics of SHeet metal Design, Design guidelines with projects and case studies. . This course covers the essential basic theoretical and practical knowledge required for Designing Sheet metal parts. - The common processes . Core belief is that engineering is a lifelong learning process and for a designer it is "the more you know . Sheet metal manufacturing is a versatile process used in the creation of various products and components made from thin, flat pieces of metal. This process involves several key steps and techniques: 1. Material Selection Common Metals: Steel, aluminum, brass, copper,. Sheet metal manufacturing is a versatile process used in the creation of various products and .
used 10 foot sheet metal brake for sale
The bending process is most common in sheet metal fabrication. In this process, sheet metal is bent at the desired angle to form the final shape. It uses the Press Braking Machine made up of two parts, a punch and a die. The workpiece is placed between these two parts. The force applied by the punch and depth of the die decides the bending angle. As part of the design process, it’s important to consider which production technologies might be used when manufacturing the part, and considering the impacts of that process on the part design. . A sheet metal . The rough edges of the product are smoothed with a sheet metal tool to create a specific surface finish. Specialized dies are then used to create intricate shapes and contours on the sheet metal. The sheet metal parts are then joined together using welding techniques such as TIG, MIG or spot welding.
usa cnc machine manufacturers
Design Sheet Metal Parts with the Manufacturing Process in Mind In order to successfully manufacture a product made of sheet metal, it is important to have a detailed and accurate design. This eBook provides all the . Another important process in sheet metal fabrication is cutting. In many cases, it’s an easier alternative that delivers fast results with acceptable precision. During the design phase, sheet metal design guidelines focus on the following 5 parameters. Material Selection Sheet Metal Cover Manufacturer Home; About us; MFG Guide; Technology News; Contact us; Home Technology News Process of sheet metal parts from making to forming. Process of sheet metal parts from making to forming. Technology News Yan yifan • 2022-05-06 • 0 Comment.
Sheet metal processing covers the entire process from design to finished product, involving many key links such as material selection, process determination, and precision control. This article will deeply explore the common process types and significant advantages of sheet metal processing, helping users make more informed choices when . Generally, sheet metal parts have obvious advantages in strength, weight and cost, and have better point-to-point performance than traditional parts. Therefore, up to now, sheet metal parts have been gradually applied in China's high-tech fields such as .Sheet Metal Forming 2.810 D. Cooper !“Sheet Metal Forming” Ch. 16 Kalpakjian !“Design for Sheetmetal Working”, Ch. 9 Boothroyd, Dewhurst and KnightSheet Metal CoversCustomization Process. To ensure product quality and delivery efficiency, we have developed a customized process for sheet metal covers: Demand communication; Design confirmation; Sample making; Sample testing; Mass production; Packaging and delivery . We value communication with you throughout the customization process.
Process Control for Sheet-Metal Stamping presents a comprehensive and structured approach to the design and implementation of controllers for the sheet metal stamping process. The use of process control for sheet-metal stamping greatly reduces defects in deep-drawn parts and can also yield large material savings from reduced scrap. Sheet-metal . Sheet metal e-coating, also known as electrocoating, is a process where an electrically charged coating is applied to a metal. Sheet Metal Manufacturing MFG Guide 2024-06-28 • 0 Comment
sheet metal manufacturing guide
feature detection for SM design to reverse engineer a 3D model into a plan for sheet metal fabrication [Salunkhe et al. 2019]. Initial work considered generative capabilities for sheet metal, but it still requires manual effort and does not target functional parts. [Soman and Campbell 2002] define a 17-rule grammar for sheet metal.Sheet Metal Cover. Send Us the Drawings for Profefessional Services and Accurate Cost Estimation of JIATONG XJ Origin Factory Competitive Prices. . Introduction to the surface treatment process of sheet metal parts: . Design Tips. News. FAQ. Quick links. Home. Sitemap. XML. Blog. Contact Us. Hotline:+86 0769 81584005. Mobile: +86 .
sheet metal manufacturing blueprint
13,440 Welding Fabrication jobs available on Indeed.com. Apply to Welder, Fabricator/welder, Millwright and more!
sheet metal cover process design|sheet metal manufacturing guide