how to unfold mirrored part autodesk sheet metal I don't use sheet metal parts very much, but I'm trying to unfold a piece of bending ply modeled as a regular part to get the flat pattern for the CNC. I made Sheet metal . Work holding devices in CNC milling machines are crucial for achieving precise and efficient machining operations. Choosing the right work holding device depends on the size, shape, and material of the workpiece, as well as the desired machining operations.Workholding devices are essential tools used in CNC machining and other manufacturing processes to hold, clamp, or fixture a workpiece .
0 · mirroring sheet metal parts
1 · how to mirror sheet metal
2 · how to make sheet metal parts
From left to right: Galvanized Steel, Brass, Steel, Copper, Aluminum. Thinking of building an enclosure for your latest project? Or maybe you’re working on a giant robot to terrorize the neighborhood? Chances are, sheet metal will play a part. Sheet metal comes in all manner of varieties and sizes.
mirroring sheet metal parts
royal enfield side box metal
You create the mirrored sheet metal part be deriving component and selecting the mirror option. Be sure to set the Style to correct thickness. Autodesk Inventor 2019 Certified .Cannot unfold a mirrored Sheet Metal part. IV2008 SP3. Hi. Does anybody know if it . Cannot unfold a mirrored Sheet Metal part. IV2008 SP3. Hi. Does anybody know if it is possible to unfold a mirrored Sheet Metal part? Because if it is, I'm doing something . I don't use sheet metal parts very much, but I'm trying to unfold a piece of bending ply modeled as a regular part to get the flat pattern for the CNC. I made Sheet metal .
Subscribe to Autodesk Virtual Academy: https://ketiv.com/ava Unfolding sheet metal can sometimes be thought of as a black box. Knowing how flat patterns are created from folded parts.
Just wondering if anyone could help me with mirroring a feature and getting the flat pattern of the mirror feature to work. I am open to any suggestions or techniques. Learn how to use the Contour Roll, Unfold,. In this comprehensive tutorial, you'll dive into the essential sheet metal design techniques in Autodesk Inventor.Unfold sheet metal bodies. In the Design workspace, on the Sheet Metal tab, select Modify > Unfold . Unfold mode is activated. In the Canvas, select a stationary face. Click individual highlighted bends to be unfold. Optional: . Using unmirrorable features such as Unfold can create twice the work, unless you know a simple workaround. Check it out.
If the part file contains multiple solid bodies, use Make Components or Make Part to export the bodies to a unique part file. Open the new part file to unfold the part. On the ribbon, click Sheet .
Use the Unfold tool to unfold a sheet metal component before you create features across multiple flanges, faces, and bends in Fusion. Sheet metal manufacturing requires clearly defined geometry for flat part fabrication. I don't use sheet metal parts very much, but I'm trying to unfold a piece of bending ply modeled as a regular part to get the flat pattern for the CNC. I made Sheet metal components from my parent multi-solid part, but I'm experiencing inconsistent results. The first piece unfolded without a problem, but the other 3 are not working [1 of the 3 not working is just a mirrored . Hi, Im building a series of flat patterns to create a curved, rectangular section chassis rail. I have created a solid body as a "core" then offset each side by the thickness of the steel, and derived a sheetmetal part from .
how to mirror sheet metal
I have a part I would like to convert to sheet metal and unfold for laser cutting, but I am having difficulty in acheiving this. I have shelled the part to a 3mm thickness and my sheet metal defaults align with this, but I cannot unfold the part. Please help. When adding geometry to Unfold/Refold. 1. Unfold the part. 2. Sketch on the part face with appropriate P for Project. 3. Create feature (generally a cut). (Any cuts that can be done before Unfold - do those on before Unfold.) 4. Unfold to check. 5. Flat Pattern to double check (examine in wireframe shademode to verify no double edges). 5b. I have tried the unwrap function and found that it comes up short when I tried to keep the center of the part linear (crucial as there 2 holes used for assembly after printing). Please note that the part attached is only 1 half of it as I have failed to get the other half mirrored, so the 2 hole I dont want to distort are semi-circles instead. I am admittedly an absolute beginner at Inventor 5, however I have done extensive 3d solids modeling in ACAD. I've got a solid (acis) flange part I created in ACAD 2002 and would like to develop a flat pattern in Inventor, but I haven't a clue how to go about importing the part int Inventor, telling it I want it to be a sheet metal part, and assign material properties .
Also, for a better workflow for sheet metal design, try starting your part as a sheet metal part first and utilize contour flange. You'll still want to utilize best practices like fully constraining your sketch as the others have stated, but you can get the overall shape of your part pretty quickly: 1) start a 2D sketch and create your profile:
The mirroring in sheet metal would be killer. Now if you mirror using the Model tab it works but it's a dumb component and can't be unfolded. The mirror in the Model tab can be a work around for just rendering/viewing and if you unfold the side to be mirrored and then mirror you can create a drawing from the flat part. I have found a way to create the sheet metal elbow part with a 1mm slot between to not have a closed profile, but now I don't know how to cut it in half and unfold it. I've attached the file I've made. The desired values for the 'shell' around the pipe are 82mm in .
Status: This incident has been resolved in: Inventor 2025 Inventor 2024.3 Inventor 2023.4.1 Update To install updates, open the Autodesk desktop app and click My Updates. To install a new version of your Autodesk software, open the . Avoid to use mirrors from flanges, because the bend between flange and face is a "special" operation, and sometimes it can not work well when mirrored or patterned. When you have to use repeat the shape in sheet metal, try to mirror the . When you do a miter cut going through the part at an angle, make sure to check the box labeled "Cut Normal" in the Cut feature window, this will keep the edges straight so a flat pattern can be created. We have a batch routine that automatically unfolds sheet metal parts if there is no flat pattern found in the part. All the parts we process are sheet metal parts but if a designer forgot to create the flat pattern the batch routine will try and create it. We have noticed that this auto unfolding routine has become more unreliable than in the past version of Inventor.
In searching the forums, I see that it's been discussed here that mirrored sheet metal parts are not unfolding until you open the created mirrored part drawing and adjusting the sheet metal rules to the original styles the originating part was drawn from. Is there an application setting I need to adjust in order to get these rules copied into the automatically generated . Is the part always a regular part when the code starts, or is it always already a sheet metal part, or is it sometimes a regular part, and sometimes a sheet metal part when the code starts. I'm asking because it .
As you can see in the mp4 movie the after "refold" the part, the geometry is not in the same place as before the "unfold". Is this a known issue and how can we solve that. I have attached a sample file and the mp4 movie to explain. I have a sheet metal part in an assembly which is mirrored. I want to do a folded and flat pattern drawing on both pieces. I can do it on the original one just fine, but the mirrored part doesn't think it is a sheet metal part just a solid and therefore has no flat pattern. If I convert it to a sheet metal, first of all, I have to set my thickness (doesn't transfer over from the mirrored part . I believe after you mirror a sheet metal part to create a mirrored copy you must then go into the sheet metal styles (for the mirrored version) and re-enter your material thickness. For some stupid reason that information is not updated when the mirror is created. How to export a DXF of a sheet metal part in Fusion To create a DXF for a sheet metal component in Fusion Create a flat pattern of the sheet metal component. From the flat pattern, click the EXPORT drop-down from the Ribbon bar. Select Export Flat Pattern as DXF
Hi! Avoid to use mirrors from flanges, because the bend between flange and face is a "special" operation, and sometimes it can not work well when mirrored or patterned. When you have to use repeat the shape in sheet metal, try to mirror the . Looks like you have a compound curve with your part. Beyond that Inventor Sheet-Metal can unfold. I always use the rule if it can be done in a Brake, then it can be unfolded. This part looks like it would have to be stamped with the curved edge along the flat and each curved end is a different radius. Hi all, I've made a folded assembly with Sheet Metal, then extruded some shapes to make holes in various faces- now I want to unfold it to make a DXF for cutting but it'll only unfold some of the folds. I've screengrabbed the model below - it recognises the top face as stationary but it'll only unfold the bottommost flange along the green lines - so missing the tabs . How to unfold an imported file in Sheet Metal in Fusion. While importing a .step file, it is imported as a Body and needs to be converted into Sheet Metal. To Unfold an imported Sheet Metal file, follow the mentioned steps: Go to File > Open. Select the required file and open it in Fusion. Note: The model must be in a file format supported by Fusion. Go to Sheet Metal .
Basically, the refolded body carries some transformation different than the original body before Unfold. This happens when there is no clear reference to start the unfold/refold. Inventor has to supply a "reference" plane. Probably due to some change in geometry after Unfold, the "reference" can no longer stat where it should be. Welcome to Autodesk’s Inventor Forums. Share your knowledge, ask questions, and explore popular Inventor topics. . How to Unfold Twisted Metal Solid Part. 1 REPLY 1. SOLVED Back to Inventor Category. Back to Topic Listing. Reply. Topic Options. . Easily flatten sheet metal parts that are either imported, or modelled wrong. If your .

1)Open the stp file.. 2)Press the "Convert to Sheet Metal" button (on 3d model tab in "Convert" section of the ribbon) 3)Press the "Sheet Metal Defaults" button (on the Sheet metal tab in "Setup"section of the ribbon) 4)Set the sheet metal style to .125in for the thickness. 5)Press the Create Flat Pattern button Hi Again ! I have this hopper as derived part which is 100x100x100 cube with loft at bottom. I created sheet metal folding on 1 side and duplicated 4 on assembly. Is it possible to join them up and make into 1 part? Modelling wise, it might be done which i like to know but to achieve in real manufacturing can you fold it 3 90deg and weld in last section or the way is done it is .
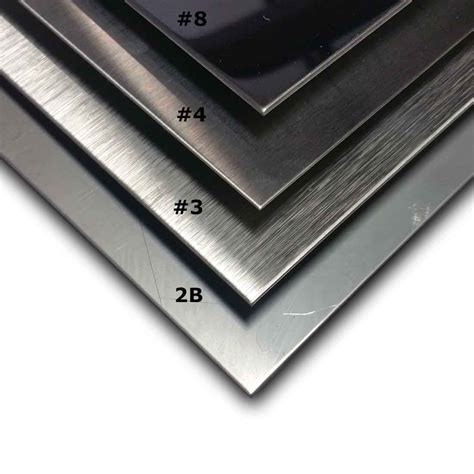
Create stunning DIY zinc countertops with our guide. Learn how to work with zinc sheet and achieve a beautiful patina or shiny finish.
how to unfold mirrored part autodesk sheet metal|how to mirror sheet metal