sheet metal stamping processes involved Metal stamping or metal pressing is a process that consists of a series of processes actually, including bending, punching, and blanking with tools and dies, coining, flanging, etc. The process gives the metal sheet the desired shape . – Smooth surface finish and high machining quality – ISO9001:2015 certification – OEM service with 15 years experiences in CNC . See more
0 · surfaces for stamping metal
1 · stamping operation in sheet metal
2 · sheet metal stamping basics
3 · sheet metal stamping at home
4 · metal stamping process step by
5 · metal stamping process flow chart
6 · how metal stamping manufacturing works
7 · automotive sheet metal stamping process
A quick nip in between, discreetly and without leaving any suspicious traces, this can be done easily with the Royal Box®! Just slide it to open and pull it in - goodbye, you germy, filthy .
Metal stamping is an incredibly versatile and efficient manufacturing process that takes flat metal sheets or coils and transforms them into precisely shaped and intricate parts. By utilizing force, pressure, and specialized tooling, .The stamping process in sheet metal involves several key steps to transform flat sheets into shaped components. It begins with designing the part and creating custom tooling, including .Metal stamping or metal pressing is a process that consists of a series of processes actually, including bending, punching, and blanking with tools and dies, coining, flanging, etc. The process gives the metal sheet the desired shape .
Below are some of these tools: Die Sets: These are custom-made templates used to shape metals during stamping. Typically, a die set consists of two parts: a punch part and a die part. .
Metal stamping is a high-volume manufacturing process that transforms flat metal sheets into specific shapes using mechanical forces. This versatile technique is crucial in various industries, including automotive, .The sheet metal stamping process is where metal sheets can be shaped and sized to the desired shape or size by applying an external force. Stamping machines and dies are used to achieve this. It’s fascinating. Seeing a simple .There are basically only three components to sheet metal stamping—the sheet metal, die, and press machine—but any single part can require multiple steps to arrive at its final form. The following guide explains a few common processes .
Titanium. The Sheet Metal Stamping Process. There are three components to sheet metal stamping: the sheet metal, the press machine, and the die. However, producing any .Precision metal stamping is an innovative process that utilizes machinery fitted with dies to transform flat sheet metal into custom shapes. It involves various processes such as punching, bending, embossing, flanging, and coining.Introduction to the sheet metal/ metal stamping industry BWC identified sheet metal and metal stamping employers among the top 10 workers’ compen-sation classifications with the highest fre-quency of claims and highest claims costs in Ohio. According to the National Council on Compensa-tion Insurance’s (NCCI’s) manual classifications, Alternatively, the sheet metal stamping process can only produce long parts if secondary processes are involved to connect shorter stamped workpieces into one, increasing both production times and costs. Budget. Roll forming is often the more expensive method as it involves a bit more manual labor, but this depends on the volume and lengths you .
A sheet metal stamping process is a metalworking process carried out at room temperature wherein parts are both cut and shaped from a parent metal strip or. . Almost always, there are multiple steps involved in the production of parts .
surfaces for stamping metal
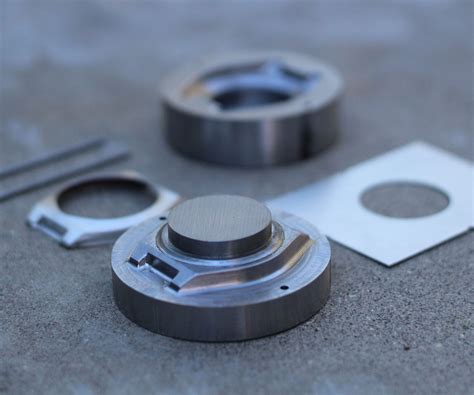
Automotive metal stamping is a manufacturing process used to create metal parts, components, and assemblies for the automotive industry. It involves the use of a stamping press, which applies high pressure to a metal sheet or strip to create the desired shape. The process is commonly used to create parts. Sheet metal stamping is one of the most important manufacturing processes, where sheet metals are transformed into diverse shapes and parts. The process is placed within a stamping press wherein sheet metals take up or more sheet metal stamping dies, creating products adapted to usage in various industrial applications, including automotive, aerospace, .
cnc tailoring machine
Sheet metal fabrication is the process of transforming sheet metal (< 1/4” thick) into finished products, structures, and components. From household appliances to transportation, commercial equipment to construction, sheet metal fabrication is critical to modern manufacturing. In this article, we cover the basics of sheet metal fabrication, from material selection to key . Numerical simulation of sheet metal forming processes has become an indispensable tool for the design of components and their forming process, in industries ranging from the automotive, to the .Metal stamping is a metal fabrication and manufacturing process that uses indentation to form various shapes, letters and patterns onto sheet metal materials.. Also known as “pressing”, some common and complex metal forming techniques associated with .
We will visit each of the processes involved in sheet metal stamping. Blanking. Blanks are simple geometric shapes punched out from the metal sheets. The shapes can be of various geometries from circles to squares. The key considerations in this process include punch-die clearance ratio and blanking force (the pressure exerted on the die), as . In the manufacturing industry, the sheet metal process is common, and sheet metal parts are used in many different industries, including consumer products, appliances, aircraft, and the automotive and aerospace sectors. Sheet Metal Operations. Following are the 9 different types of sheet metal operations: Shearing Operations; Blanking Operations This blog will explore sheet metal forming, the various operations involved in this intricate process, and its numerous advantages. Key Operations in Sheet Metal Stamping. There are several operations involved in sheet metal stamping, including the following: Bending
stamping operation in sheet metal
Stainless steel sheet metal processing offers a range of advantages that make it a popular choice for various applications. Some of the key advantages of stainless steel sheet metal processing include: Corrosion Resistance: Stainless steel is highly resistant to corrosion, making it suitable for applications in harsh environments, such as marine, chemical, and food processing industries.As a degreed Mechanical Engineer (BS) and Industrial Engineer (MS) and growing up in and around tool shops (uncle was a Master Tool and Die Maker), there is both engineering and shop time involved. Tool and Die makers can certainly design dies, but as they get more complex, more engineering analysis gets involved, usually after a die failure or .
Process Control For Sheet Metal Stamping Process Modeling Controller Design And Shop Floor Implementation Advances In Industrial Control Michael Seilmaier . The reader would typically be involved in the design, implementation and upgrading of industrial control systems. Mathematical theory has been kept to a minimum with .The sheet metal fabrication process is an intricate journey from raw metal to a finished product. It involves various steps, ensuring the final product meets specific standards and functions. It involves various steps, ensuring the final product meets specific standards and functions.
Sheet metal forming tools play an important role in the manufacturing of many products. With shorter product life cycles and demand for shorter time to market for new products, the process for .
Cutting, bending, stamping, punching, welding, and finishing are the fundamental processes involved in manufacturing sheet metal products. In a little while, we shall get into the specifics of each of these methods. Manufacturing .Stamping of sheet metal is a process based on permanent deformation by cold forming to produce a variety of complex three-dimensional shapes. . these are the main processes involved to manufacture metal parts in all industries fields: automotive, household appliances, medical, logistic and plant system sectors and infinite others. .
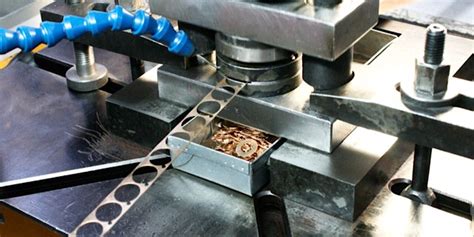
Stamping dies are the tools that shape and cut sheet metal parts. They are commonly developed using computer-aided design (CAD) software and analytical programs to create and prove-out highly accurate, unambiguous designs. These designs are then translated into stamping dies by skilled craftsmen, known as diemakers. Once these stamping dies are mounted into presses, .The numerical simulation of sheet metal forming processes has become an indispensable tool for the design of components and their forming processes. This role was attained due to the huge impact in reducing time to market and the cost of developing new components in industries ranging from automotive to packing, as well as enabling an improved understanding of the .
The stamping process is also known as pressing. It includes placing flat sheet metals in a press and converting them into a coil or a blank. Here, a tool or die surface attain a specific shape. So, several techniques featured in this stamping process. What is the Sheet Metal Stamping Process? Here we will discuss how to stamp sheet metal.
sheet metal stamping basics

When it comes to custom stainless steel and aluminum sheet metal fabrication, there are several important processes involved. These processes play a crucial role in shaping and forming the metal .Stamping (also known as pressing) is the process of placing flat sheet metal in either blank or coil form into a stamping press where a tool and die surface forms the metal into a net shape. Stamping includes a variety of sheet-metal forming manufacturing processes, such as punching using a machine press or stamping press , blanking, embossing .

Step#3 Setting Up the Stamping Press. After the die is designed and developed, setting up the stamping press is the subsequent phase. As the global metal stamping market is projected to grow at a CAGR of 4.1% by 2032, according to Polaris, optimizing the press setup becomes even more critical for maintaining competitiveness.Here’s how the setup process unfolds:Sheet metal manufacturing processes encompass a range of techniques aimed at shaping and forming metal sheets into desired products. In this article, we will explore some of the key processes involved in sheet metal manufacturing. 1. Cutting: . Stamping: Stamping is a high-volume manufacturing process used to produce large quantities of .
Cutting, bending, stamping, punching, welding, and finishing are the fundamental processes involved in manufacturing sheet metal products. In a little while, we shall get into the specifics of each of these methods. Manufacturing using .
Explore the fundamental steps and processes involved in metal stamping, showcasing how this manufacturing technique transforms raw metal materials into preci.
cnc stainless steel connection parts
cnc steel machining manufacturer
Antique Whitman's candy tin box made in the USA. The box is ideal for storing candy, cookies, or any other small treats.
sheet metal stamping processes involved|stamping operation in sheet metal