default bend radius for sheet metal Assuming you used an inside bend radius smaller than the material thickness, the K-factor (or neutral factor, if you prefer) in our cheesy example would be 0.33 for an air bend and 0.42 for a bottom bend, both gradually increasing to 0.5 for . I'm installing a PVC 6x6 junction box on the outside of a house. I can't find any requirements in the code but it's about 6" off the ground. Anyone ran into problems with clearance from finished grade?
0 · sheet metal minimum bend length
1 · sheet metal inside bend radius
2 · sheet metal bend radius guide
3 · bending steel plate minimum radius
4 · bend radius vs material thickness
5 · bend radius sheet metal chart
6 · 304 stainless steel bend radius
7 · 304 stainless minimum bend radius
A concrete distribution box is the traffic director of your septic system. It’s critical for managing the flow of wastewater from the septic tank to your drain field. This box ensures that effluent is evenly distributed across the drain field, preventing overloading and .
Your best bet when designing formed parts is to use the industry standard bend radius of 0.030”. This measurement ensures consistent, high-quality parts with solid structural integrity. We use 0.030" for all material .
A typical recommendation is 1t for all sheet metal parts, which means the smallest bend radius should be at least equal to the sheet thickness. For example, if the thickness of the sheet is 2mm, the minimum bend radius .
sheet metal minimum bend length
sheet metal inside bend radius
The sheet metal bending radius is a critical value in sheet metal drawing that can be difficult to determine during the actual processing. This radius is dependent on the material thickness, the pressure of the press brake .RECOMMENDED MINIMUM BEND RADII FOR 90-DEGREE COLD FORMING OF SHEET The radii listed are the minimum recommended for bending sheets and plates without fracturing in .Assuming you used an inside bend radius smaller than the material thickness, the K-factor (or neutral factor, if you prefer) in our cheesy example would be 0.33 for an air bend and 0.42 for a bottom bend, both gradually increasing to 0.5 for . Here’s a CAD tip: The default kerf width is equal to the material thickness. This tip is important for punched parts. Smaller kerf widths, as small as the cutting orifice, are practical for laser- cut or waterjet-cut parts. An accurate .
In steel between 0.5 and 0.8 in. thick, grade 350 and 400 may have a minimum bend radius of 2.5 times the material thickness when transverse bending, while longitudinal bending may require a minimum bend radius that’s . We recommend a minimum bend radius of 1t for all sheet metal parts. Thus the smallest radius of any bend in a sheet should be at least equal to the thickness of the sheet. For example, if the thickness of the sheet is 1 mm, . The default bend radius in SOLIDWORKS is 0.100”, a specification that requires specialty tooling to achieve. We recommend changing the bend radius to 0.030”, the industry standard for sheet metal with a thickness of up to .Consider what minimum bend size you require (Only consider lines that meet your minimum bend requirement). You may choose any bend radius on this line(s). If you have multiple options, optimize your choice.
Your best bet when designing formed parts is to use the industry standard bend radius of 0.030”. This measurement ensures consistent, high-quality parts with solid structural integrity. We use 0.030" for all material thicknesses up to 0.125" (⅛") and increase the bend radius for thicker materials. A typical recommendation is 1t for all sheet metal parts, which means the smallest bend radius should be at least equal to the sheet thickness. For example, if the thickness of the sheet is 2mm, the minimum bend radius should be 1t which is 2mm. The sheet metal bending radius is a critical value in sheet metal drawing that can be difficult to determine during the actual processing. This radius is dependent on the material thickness, the pressure of the press brake machine, and the width of .
RECOMMENDED MINIMUM BEND RADII FOR 90-DEGREE COLD FORMING OF SHEET The radii listed are the minimum recommended for bending sheets and plates without fracturing in a standard press brake with air bend dies. Other types of bending operations may require larger radii or permit smaller radii.Assuming you used an inside bend radius smaller than the material thickness, the K-factor (or neutral factor, if you prefer) in our cheesy example would be 0.33 for an air bend and 0.42 for a bottom bend, both gradually increasing to 0.5 for larger bend radii. Here’s a CAD tip: The default kerf width is equal to the material thickness. This tip is important for punched parts. Smaller kerf widths, as small as the cutting orifice, are practical for laser- cut or waterjet-cut parts. An accurate flat layout helps .
In steel between 0.5 and 0.8 in. thick, grade 350 and 400 may have a minimum bend radius of 2.5 times the material thickness when transverse bending, while longitudinal bending may require a minimum bend radius that’s 3.75 times the material thickness (see Figure 1). We recommend a minimum bend radius of 1t for all sheet metal parts. Thus the smallest radius of any bend in a sheet should be at least equal to the thickness of the sheet. For example, if the thickness of the sheet is 1 mm, the minimum bend radius should be 1 mm. The default bend radius in SOLIDWORKS is 0.100”, a specification that requires specialty tooling to achieve. We recommend changing the bend radius to 0.030”, the industry standard for sheet metal with a thickness of up to 0.125”. For thicker metals, we can help you determine the appropriate bend radius. To set a bend radius in SOLIDWORKS:Consider what minimum bend size you require (Only consider lines that meet your minimum bend requirement). You may choose any bend radius on this line(s). If you have multiple options, optimize your choice.
sheet metal bend radius guide
Your best bet when designing formed parts is to use the industry standard bend radius of 0.030”. This measurement ensures consistent, high-quality parts with solid structural integrity. We use 0.030" for all material thicknesses up to 0.125" (⅛") and increase the bend radius for thicker materials. A typical recommendation is 1t for all sheet metal parts, which means the smallest bend radius should be at least equal to the sheet thickness. For example, if the thickness of the sheet is 2mm, the minimum bend radius should be 1t which is 2mm. The sheet metal bending radius is a critical value in sheet metal drawing that can be difficult to determine during the actual processing. This radius is dependent on the material thickness, the pressure of the press brake machine, and the width of .RECOMMENDED MINIMUM BEND RADII FOR 90-DEGREE COLD FORMING OF SHEET The radii listed are the minimum recommended for bending sheets and plates without fracturing in a standard press brake with air bend dies. Other types of bending operations may require larger radii or permit smaller radii.
Assuming you used an inside bend radius smaller than the material thickness, the K-factor (or neutral factor, if you prefer) in our cheesy example would be 0.33 for an air bend and 0.42 for a bottom bend, both gradually increasing to 0.5 for larger bend radii. Here’s a CAD tip: The default kerf width is equal to the material thickness. This tip is important for punched parts. Smaller kerf widths, as small as the cutting orifice, are practical for laser- cut or waterjet-cut parts. An accurate flat layout helps .
In steel between 0.5 and 0.8 in. thick, grade 350 and 400 may have a minimum bend radius of 2.5 times the material thickness when transverse bending, while longitudinal bending may require a minimum bend radius that’s 3.75 times the material thickness (see Figure 1).
We recommend a minimum bend radius of 1t for all sheet metal parts. Thus the smallest radius of any bend in a sheet should be at least equal to the thickness of the sheet. For example, if the thickness of the sheet is 1 mm, the minimum bend radius should be 1 mm.
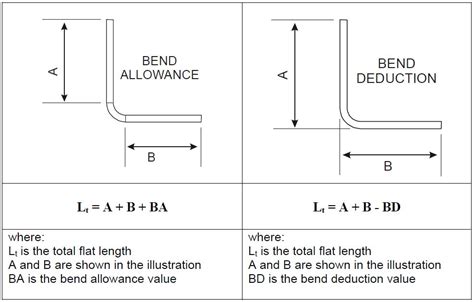
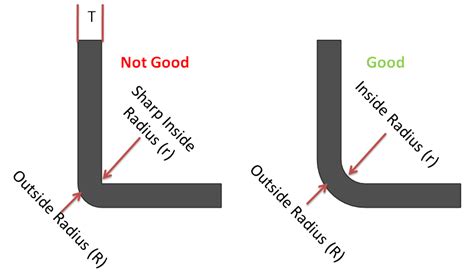
bending steel plate minimum radius

bend radius vs material thickness
bend radius sheet metal chart
304 stainless steel bend radius
Big-box retailers are retail giants, occupying massive buildings that often span over 50,000 square feet. Walmart, Home Depot, and Ikea are a few examples. Originally, warehouse clubs like Costco pioneered the big-box concept, offering consumers a plethora of products at unbeatable prices.
default bend radius for sheet metal|sheet metal inside bend radius