sheet metal working process ppt This document discusses various sheet metal processes including cutting, . Because the termination box on an electric motor looked very similar, it was called (probably) "that there picker head thang on the 'lectric motor"!
0 · sheet metal stamping process pdf
1 · sheet metal manufacturing process ppt
2 · sheet metal calculations pdf
3 · sheet metal bending machine ppt
4 · sheet metal basic ppt
5 · sheet metal basic drawing
6 · rolling direction of sheet metal
7 · mechanical properties of sheet metal
So now you can get a shock from the box, outlet, and the case (if its metal) of whatever you plug into the outlet. The ground would need to continue on to the panel's ground bar to complete the circuit, trip the breaker and actually .
sheet metal stamping process pdf
Rubber Pad Forming (RPF) RPF is a metalworking process where sheet metal is pressed between a die and a rubber block, made of polyurethane. Under pressure, the rubber .
The process is normally a cold working process using a set of punch and die. .
This document discusses various sheet metal processes including cutting, .This document discusses various sheet metal processes including cutting, .
The process is normally a cold working process using a set of punch and die. Bending - straining of a metal sheet to form an angle bend. Drawing - forming a sheet into a hollow or concave shape. Shearing - not a . This document discusses various sheet metal processes including cutting, forming, bending, drawing, and stretching operations. Some key points: 1. Sheet metal work involves forming metal sheets 3-5mm thick into parts . Sheet metal working involves cutting, bending, drawing, and other forming operations to shape metal sheets. The processes include shearing, blanking, and punching, with various tools like punches and dies. Clearance, .The cutting and bending processes are important for manufacturing sheet metal parts for a wide range of applications. The document discusses various sheet .
sheet metal manufacturing process ppt
Sheet metal working involves forming and cutting operations performed on metal sheets, strips, and coils using presses and tools like punches and dies. Common sheet metal operations include bending, drawing, shearing, blanking, piercing, .Objectives. By the end of today you should be able to. .describe different forming processes, when they might be used, and compare their production rates, costs and environmental . In this article, you will learn the 9 different types of sheet metal operations with diagrams. Also, you can download the pdf file of this post. What is the Sheet Metal Process?
This document discusses various sheet metal processes including cutting, forming, bending, drawing, and stretching operations. Some key points: 1. Sheet metal work involves forming metal sheets 3-5mm thick into parts .1 SHEET METAL WORKING. 2 Introduction Sheet metal is simply metal formed into thin and flat pieces. It is one of the fundamental forms used in metalworking, and can be cut and bent into . 2. Sheet Metalworking Defined Cutting and forming operations performed on relatively thin sheets of metal Thickness of sheet metal = 0.4 mm (1/64 in) to 6 mm (1/4 in) Thickness of plate stock > 6 mm Operations usually .
In the manufacturing industry, the sheet metal process is common, and sheet metal parts are used in many different industries, including consumer products, appliances, aircraft, and the automotive and aerospace sectors. .
7. 5: Notching: This is cutting operation by which metal pieces are cut from the edge of the sheet , strip or blank. 6: Perforating: This is a process by which multiple holes are very small and close together are cut in a flat sheet . 4. 1.0 Introduction Sheet metal is simply metal formed into thin and flat pieces. Sheet metal is essentially metal pressed into sheets. These sheets are used at various places. These sheets can be bent, cut and molded into any shape for use anywhere. Sheet metal is generally produced in sheets by reducing the thickness of work piece by compressive forces . Sheet Metal Forming - Download as a PDF or view online for free. Submit Search. . It is a process where the punch and the work piece touches the bottom of the die. This makes a controlled change of angle with very little spring back. The inner radius of work piece should be a minimum of a 1 material thickness. In bottom bending, spring back .
Classification of metal working processes : Download: 22: Mechanics of metalworking and analysis methods : Download: 23: Determination of flow stresses in metal working : Download: 24: Hot working and cold working : Download: 25: Metallurgical considerations in metal forming : Download: 26: Introduction and classification of forging processes . 1. Metal forming processes Metal forming: Large set of manufacturing processes in which the material is deformed plastically to take the shape of the die geometry. The tools used for such deformation are called die, punch etc. depending on the type of process. Plastic deformation: Stresses beyond yield strength of the workpiece material is required.
Introduction Sheet metal is simply metal formed into thin and flat pieces. It is one of the fundamental forms used in metalworking, and can be cut and bent into a variety of different shapes. Countless everyday objects are constructed of the material. Thicknesses can vary significantly, although extremely thin thicknesses are considered foil or leaf, and pieces thicker . 8. Salient points about rollingSalient points about rolling Rolling is the most extensively used metal formingRolling is the most extensively used metal forming process and its share is roughly 90%process and its share is roughly 90% The material to be rolled is drawn by means of frictionThe material to be rolled is drawn by means of friction into the two revolving .
4 5.1. EFFECT OF HOT WORKING ON MECHANICAL PROPERTIES OF METALS 1- This process is generally performed on a metal held at such a temperature that the metal does not work-harden 2. Raising the metal temperature lowers the stresses required to produce deformations and increases the possible amount of deformation 3. Surface finish of hot worked .
sheet metal calculations pdf
This document provides an overview of press working and various sheet metal forming operations. It defines press working as a chipless manufacturing process that uses a press machine to form sheet metal components by applying force. . ALA Presentation On Press introduction & Operation Branch:-Mechanical Sem.:-6 Div:-D Prepared By:- Guided By .Manufacturing Processes Ch.6 (20) Sheet Metal Working - Free download as Powerpoint Presentation (.ppt), PDF File (.pdf), Text File (.txt) or view presentation slides online. The document discusses various sheet metal working processes including cutting operations like shearing, blanking, and punching and describes how they work. It also covers bending .Introduction Sheet metal is simply metal formed into thin and flat pieces. It is one of the fundamental forms used in metalworking, and can be cut and bent into a variety of different shapes. Countless everyday objects are constructed of the material. Thicknesses can vary significantly, although extremely thin thicknesses are considered foil or leaf, and pieces thicker . Metal work safety - Download as a PDF or view online for free . In the MIG process, the electrode is a consumable metal wire which automatically feeds into the weld, providing filler material. The MIG wire control, cooling passages, and current control are combined in a compact welding gun. Once adjusted for the job at hand, the MIG outfit is .
Fundamentals of metal working - Download as a PDF or view online for free. . Metalworking is the process of working with metals to create individual parts, assemblies, or large-scale structures. 3. . Sheet metal . Sheet Metal Forming. Lecture 6. SHEET METAL WORKING. Cutting Operations Bending Operations Drawing Other Sheet Metal Forming Operations. . An Image/Link below is provided (as is) to download .Sheet Metal Forming 2.810 D. Cooper !“Sheet Metal Forming” Ch. 16 Kalpakjian !“Design for Sheetmetal Working”, Ch. 9 Boothroyd, Dewhurst and Knight 8. SHEARING • It is a process of cutting a straight line across a strip, sheet • Metal is placed between upper punch & lower die. • Pressure is applied, plastic deformation takes place. • As the pressure is continued, the fracture or crack start at the cutting edge of the punch • As the punch descends further, the small fractures meet & the metal is then sheared.
3. Sheet Metal Working Defined Cutting and forming operations performed on relatively thin sheets of metal Thickness of sheet metal = 0.4 mm (1/64 in) to 6 mm (1/4 in) Thickness of plate stock > 6 mm The sheet or plate stock in metal working is produced by rolling. Operations usually performed as cold working. 3
Sheet metal Forming Process - Download as a PDF or view online for free. . • Download as PPT, PDF . to Building a Sheet Metal Chassis for your 2.810 Car Using Solidworks”, by Eddy Reif 5. “Design for Sheetmetal Working”, Ch. 9 . 1) Incremental sheet forming is an innovative metal forming process where a spherical tool is used to push a sheet into a desired shape without the need for dies. 2) The document provides an overview of the incremental sheet forming process, including its history and development, common methods like single-point and two-point forming .Sheet metal forming process Chapter 7 Introduction Sheet metal forming operations produce a wide range of consumer and industrial products, such as metal desks, appliances, aircraft fuselages, car bodies, and kitchen utensils. Sheet-metal forming also called press working, press forming or stamping, is among the most important of metalworking processes, dating back to . ppt on Sheet metal process - Download as a PDF or view online for free . punch begins to push into work, causing plastic deformation; Sheet Metal Cutting 8. ©2007 John Wiley & Sons, Inc. M P Groover, Fundamentals of Modern Manufacturing 3/e Figure 20.1 Shearing of sheet metal between two cutting edges: (3) punch compresses and penetrates .
Sheet Metal Working. Products: automotive fenders washers stamped parts channels. . Group 9 Presentation. Sheet-Metal Forming Processes. Scott Currie Jared Adams Taylor Grisham Yien- Sheng Ao Joe Butner. Extrusion and Drawing of Metals. . Sheet metal forming process is carried out in the plane of the sheet by tensile forces with a high . Sheet metal working - Download as a PDF or view online for free. Submit Search. . This process involves cutting sheet metal by subjecting it to shear stress, usually between punch and die. The major variables in this process are: Punch force Speed of punch, lubrications Edge condition of the sheet Punch and die materials. Shearing 12/31/2016 . 8. Common Welding ProcessesCommon Welding Processes • GMAW- Gas Metal Arc Welding, sometimes call Mig uses the heat of an electric arc between a continuous bare wire filler metal electrode and the work. Shielding is obtained entirely from an externally supplied inert gas (argon or helium) or reactive gases (C02 o 02) or a combination thereof.6 iii)Embossing-The operation of giving impression of figures, letter or designs on sheet metal part is known as embossing. Sheet metal embossing is a stamping process for producing raised or sunken designs or relief in sheet metal. This process can be made by means of matched male and female roller dies, or by passing sheet or a strip of metal between rolls of the desired pattern.
sheet metal bending machine ppt
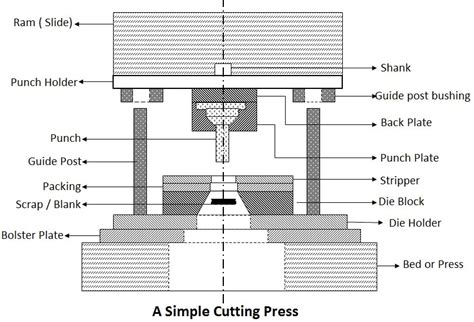
electrical box thermostat steel plate
Why use plastic electrical boxes? Plastic electrical boxes are used for several reasons. They are lightweight, cost-effective, and easy to handle. It is convenient to create holes in the back or sides of these boxes. Although PVC can melt under extreme heat, it .
sheet metal working process ppt|sheet metal calculations pdf