complex sheet metal bending Bending is a fundamental process in sheet metal working that involves deforming a metal workpiece into a desired shape by applying force between two tools by a press brake: an upper tool (known as a punch) and a bottom tool (known as a . Shop at Best Buy for USB hubs to connect additional devices.
0 · types of sheet metal bending
1 · sheet metal bending standards
2 · sheet metal bending near me
3 · sheet metal bending guidelines
4 · sheet metal bending basics
5 · bending sheet metal by hand
6 · bending sheet metal at home
7 · bending galvanized sheet metal
$29.99
This Komaspec guide provides an overview of the main sheet metal bending processes, the advantages and disadvantages of each, basic design considerations with sheet metal bending .
Sheet metal bending is a pivotal process in the realm of metal fabrication, transforming flat sheets into angular, complex structures through precise deformation. It's fascinating how a simple concept, bending, can be so integral .
Sheet metal bending refers to the fundamental process in metalworking that involves taking flat metal sheets and shaping them into three-dimensional items by applying force. Sheet metal bending is common .
Sheet metal bending is one of the most fundamental fabrication processes in the metal manufacturing industry. It’s also one of the most underrated. When product developers and engineers need components with .Bending is a fundamental process in sheet metal working that involves deforming a metal workpiece into a desired shape by applying force between two tools by a press brake: an upper tool (known as a punch) and a bottom tool (known as a . Imagine bending sheet metal without leaving a single mark or scratch. In this article, we explore innovative techniques for mark-free sheet metal bending, addressing challenges like friction, material hardness, and. Sheet metal bending is a fundamental forming process that alters the geometry of a metal sheet or panel by creating angular changes along a linear axis. This versatile technique can produce a wide range of profiles, including V-shapes, U-shapes, and more complex configurations, enabling the fabrication of various components for industries such .
This Komaspec guide provides an overview of the main sheet metal bending processes, the advantages and disadvantages of each, basic design considerations with sheet metal bending and material selection information.Sheet metal bending is a pivotal process in the realm of metal fabrication, transforming flat sheets into angular, complex structures through precise deformation. It's fascinating how a simple concept, bending, can be so integral in shaping components for myriad industries, from automotive to aerospace.
Sheet metal bending refers to the fundamental process in metalworking that involves taking flat metal sheets and shaping them into three-dimensional items by applying force. Sheet metal bending is common throughout various industries, including manufacturing, construction, automotive, and aerospace. Learn more about the process below. Sheet metal bending is one of the most fundamental fabrication processes in the metal manufacturing industry. It’s also one of the most underrated. When product developers and engineers need components with complex geometries, they usually turn to CNC machining, stamping, or forging for their metal parts.Bending is a fundamental process in sheet metal working that involves deforming a metal workpiece into a desired shape by applying force between two tools by a press brake: an upper tool (known as a punch) and a bottom tool (known as a V-die).
Bending sheet metal is a meticulous process. It involves a series of steps, starting from picking the correct type of metal, marking the bend lines, securing the metal on a bending brake, and finally applying the right amount of pressure to make the bend. How do you achieve precise bends in sheet metal? Understanding the molds and techniques behind this process is crucial. This article delves into various bending methods, from free bending to corrective bending, highlighting their applications and advantages.Learn essential custom sheet metal bending techniques and tips for designing and producing high-quality metal parts. Discover best practices, design guidelines, and practical advice for successful sheet metal bending. . This process can create some complex parts, but it does have a limit - you cannot bend angles over 130°. Also, the bend . Imagine bending sheet metal without leaving a single mark or scratch. In this article, we explore innovative techniques for mark-free sheet metal bending, addressing challenges like friction, material hardness, and.
aluminum truss fabrication
Sheet metal bending is a fundamental forming process that alters the geometry of a metal sheet or panel by creating angular changes along a linear axis. This versatile technique can produce a wide range of profiles, including V-shapes, U-shapes, and more complex configurations, enabling the fabrication of various components for industries such .This Komaspec guide provides an overview of the main sheet metal bending processes, the advantages and disadvantages of each, basic design considerations with sheet metal bending and material selection information.
Sheet metal bending is a pivotal process in the realm of metal fabrication, transforming flat sheets into angular, complex structures through precise deformation. It's fascinating how a simple concept, bending, can be so integral in shaping components for myriad industries, from automotive to aerospace.
Sheet metal bending refers to the fundamental process in metalworking that involves taking flat metal sheets and shaping them into three-dimensional items by applying force. Sheet metal bending is common throughout various industries, including manufacturing, construction, automotive, and aerospace. Learn more about the process below.
always hot junction box
Sheet metal bending is one of the most fundamental fabrication processes in the metal manufacturing industry. It’s also one of the most underrated. When product developers and engineers need components with complex geometries, they usually turn to CNC machining, stamping, or forging for their metal parts.Bending is a fundamental process in sheet metal working that involves deforming a metal workpiece into a desired shape by applying force between two tools by a press brake: an upper tool (known as a punch) and a bottom tool (known as a V-die).Bending sheet metal is a meticulous process. It involves a series of steps, starting from picking the correct type of metal, marking the bend lines, securing the metal on a bending brake, and finally applying the right amount of pressure to make the bend. How do you achieve precise bends in sheet metal? Understanding the molds and techniques behind this process is crucial. This article delves into various bending methods, from free bending to corrective bending, highlighting their applications and advantages.
types of sheet metal bending
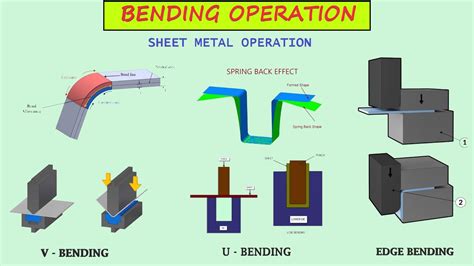
sheet metal bending standards
aluminum sheet metal thickness sizes
As someone pointed out not all devices will accept stranded but if they can then yes you can wrap the standed wire around the terminal of the device. A good trick is to strip the wire but don't remove the jacket until you wrap the wire around the screw.
complex sheet metal bending|types of sheet metal bending