different types of sheet metal joints The various joints in metal sheets are lap joint, Seam Joint, standing seam joint, grooved seam joint, corner joint, and double corner seam joint. How are sheet metals joined together? Sheet metal is joined together . Learning how to read well pump wiring diagrams is necessary to install a well pump properly. Deep submersible well pumps will be either 2-wire or 3-wire well pumps, and 3-wire well pumps will need a separately installed control box.
0 · types of sheet metal seams
1 · sheet metal overlap joint
2 · sheet metal joints pdf
3 · sheet metal joints and seams
4 · sheet metal clinching joint
5 · interlocking sheet metal joints
6 · different types of metal joints
7 · different joining methods for metal
basics of how to solder using muriatic acid, cFLUX, map gas, and tri-bar solder.
There are five common types of sheet metal joints that are extremely common across the industry, all with varying uses and advantages. The various joints in metal sheets are lap joint, Seam Joint, standing seam joint, grooved seam joint, corner joint, and double corner seam joint. How are sheet metals joined together? Sheet metal is joined together .
Sheet metal joining refers to the process of connecting different sheet metal parts through specific techniques during sheet metal fabrication, aiming to achieve the functionality and performance of the overall structure. There are five major welding joint types: butt joint, tee joint, corner joint, lap joint and edge joint. Butt joints are the most common and can be made in various ways depending on factors like groove shape and width. To determine the best weld for a joint, we’ll evaluate the length of the seam that needs to be welded as well as the material type and thickness. If you call out a particular weld joint type and welding method, we’ll do our best .
We’ll cover the following welding joint types in this guide: Butt Joint: A basic welding joint used when joining two pieces of metal edge-to-edge. Corner Joint: A joint employed when joining two pieces of metal at a 90 . Today we will try to add some new and/or improved knowledge to your brain bank by investigating together with the 5 most commonly utilized welding joints in an easy-to-read text. This joint is simple in preparation and . Learn how sheet metal joints are made and used in the HVAC sheet metal industry to make air conditioning ductwork.
There are five common types of sheet metal joints that are extremely common across the industry, all with varying uses and advantages.Sheet metal joining operation is crucial part of the sheet metal fabrication process. Joint reliability depends on its type, sheet metal material, and manufacturing process. This article covers various types of sheet metal joining techniques, their advantages, disadvantages, and applications. Discover the 7 most common sheet metal joint techniques that include riveted, welded, and adhesive joint types for appropriate enhancement of structural rigidity and effectiveness in your projects.
The various joints in metal sheets are lap joint, Seam Joint, standing seam joint, grooved seam joint, corner joint, and double corner seam joint. How are sheet metals joined together? Sheet metal is joined together through welding, riveting, adhesive bonding, or using mechanical fasteners.
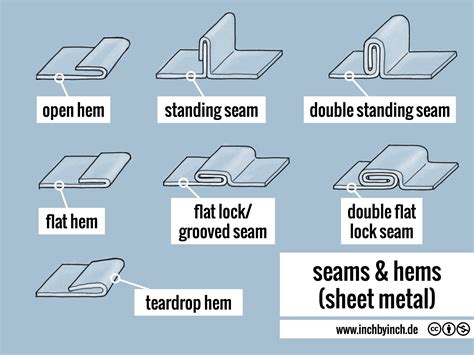
types of sheet metal seams
Sheet metal joining refers to the process of connecting different sheet metal parts through specific techniques during sheet metal fabrication, aiming to achieve the functionality and performance of the overall structure. There are five major welding joint types: butt joint, tee joint, corner joint, lap joint and edge joint. Butt joints are the most common and can be made in various ways depending on factors like groove shape and width. To determine the best weld for a joint, we’ll evaluate the length of the seam that needs to be welded as well as the material type and thickness. If you call out a particular weld joint type and welding method, we’ll do our best to defer to your preference. We’ll cover the following welding joint types in this guide: Butt Joint: A basic welding joint used when joining two pieces of metal edge-to-edge. Corner Joint: A joint employed when joining two pieces of metal at a 90-degree angle, forming a corner.
Today we will try to add some new and/or improved knowledge to your brain bank by investigating together with the 5 most commonly utilized welding joints in an easy-to-read text. This joint is simple in preparation and when welded correctly, it is unbelievably strong. Learn how sheet metal joints are made and used in the HVAC sheet metal industry to make air conditioning ductwork.
There are five common types of sheet metal joints that are extremely common across the industry, all with varying uses and advantages.
Sheet metal joining operation is crucial part of the sheet metal fabrication process. Joint reliability depends on its type, sheet metal material, and manufacturing process. This article covers various types of sheet metal joining techniques, their advantages, disadvantages, and applications. Discover the 7 most common sheet metal joint techniques that include riveted, welded, and adhesive joint types for appropriate enhancement of structural rigidity and effectiveness in your projects. The various joints in metal sheets are lap joint, Seam Joint, standing seam joint, grooved seam joint, corner joint, and double corner seam joint. How are sheet metals joined together? Sheet metal is joined together through welding, riveting, adhesive bonding, or using mechanical fasteners. Sheet metal joining refers to the process of connecting different sheet metal parts through specific techniques during sheet metal fabrication, aiming to achieve the functionality and performance of the overall structure.
There are five major welding joint types: butt joint, tee joint, corner joint, lap joint and edge joint. Butt joints are the most common and can be made in various ways depending on factors like groove shape and width. To determine the best weld for a joint, we’ll evaluate the length of the seam that needs to be welded as well as the material type and thickness. If you call out a particular weld joint type and welding method, we’ll do our best to defer to your preference. We’ll cover the following welding joint types in this guide: Butt Joint: A basic welding joint used when joining two pieces of metal edge-to-edge. Corner Joint: A joint employed when joining two pieces of metal at a 90-degree angle, forming a corner.

sheet metal overlap joint
Still, it’s possible to weld thin sheet metal using the MIG (GMAW), TIG (GTAW), and stick (SMAW) processes. But MIG and TIG provide the best results. This article will teach you how to weld thin gauge metal using each arc welding process and present the common pitfalls beginners make.
different types of sheet metal joints|sheet metal joints and seams